Top Blogs of 2023: Basics of Starting a Feed Mill
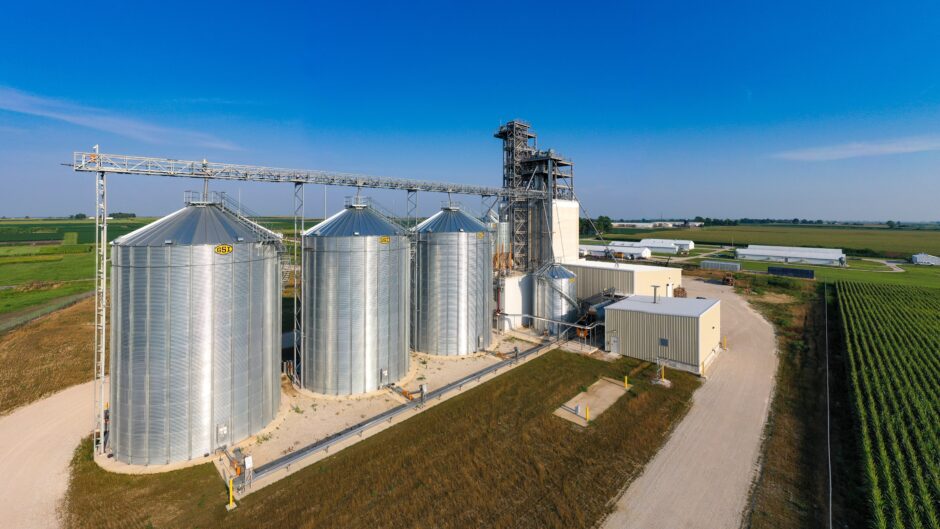
To finish off an exciting and productive 2023, we want to share with you one of our most viewed and most shared blogs of the year!
Basics of Starting a Feed Mill
Feed milling is the process of grinding and processing feed ingredients into a form that is suitable for animal consumption. The feed milling process can be divided into five main stages: raw material handling, grinding, mixing, pelleting, and cooling. Feed milling is a critical step in the production of animal feed, as it creates a uniform mixture that meets animal nutritional requirements and is easy for animals to digest. Before embarking on the design and construction of a Feed Mill, several questions will need to be answered by the customer. Below are some of the more pertinent ones:
- Target Industry: What category of animal (poultry, pigs, cattle, aquatic lifeforms, or pets) is the feed being developed for? This will usually determine the ingredients to be processed, and the product characteristics necessary for certain animal diets.
- Raw Materials: The state and nature of the raw materials to be used in feed production. This dictates whether the feed mill will require raw material pre-processing steps such as cleaning, destoning, size reduction, pre-conditioning etc.
- Capacity: How much feed will the mill produce? This directly impacts the size and layout of processing equipment employed in converting raw materials into products.
- Facilities: Will the feed mill be housed in an existing building (brownfield) or will a new building be constructed to house the mill (greenfield)? The footprint and available head space in the facility will impact whether the plant layout uses a vertical or horizontal set-up.
- Waste: Plans for dealing with waste generated during processing. For example, foreign material removed during cleaning of raw materials.
- Electricity: Available power in terms of voltage, frequency and phase, and proximity of power source to the proposed site of the feed mill.
- Air: The need for conditioning the air quality in the facility, as this impacts processing equipment such as pneumatic conveyors, coolers, dryers, air compressors etc. In some cases, it may also be a regulatory requirement that the air be conditioned to a set specification.
- Water and Steam: The quality and amount of water and steam to be made readily available at the site will depend on several factors. A major factor is whether the raw materials will need to be preconditioned before the extrusion or pelleting stages.
- By-Products: Plans for dealing with by-products produced during processing of raw materials. For example, if the final product is to be made from an oilseed and requires reduced fat content. The oil by-product generated during the fat reduction step (for example mechanical pressing) may need further processing.
- Products: What are the required characteristics of the final product that will impact the processing steps utilized in the feed mill? This will also determine if additional processing steps such as pressing, shaping, coating, cooling, packaging etc. will be required.