Drive Costs Down & Profits Up with our Service Plus Program
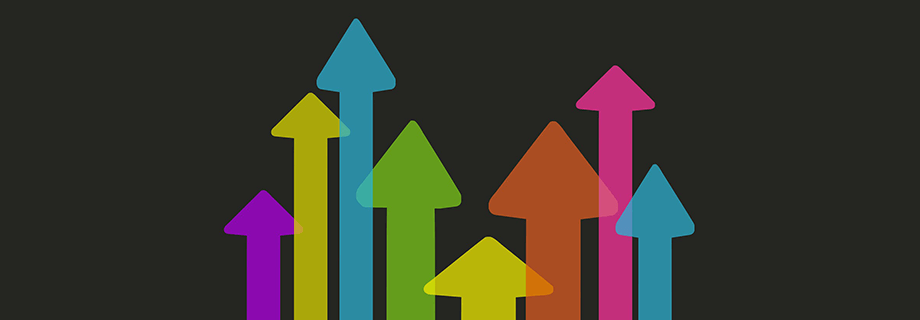
In my 35 years with Insta-Pro, customer service has been and always will be my top priority. I have taken countless phone calls directed at helping our customers solve problems and worked with the rest of my team to identify ways we can provide timely support to our customers. This is how the Service Plus Program came about.
Proper operating procedures and parts replacement are critical to maintaining maximum production and quality control. Whether you are a new operation or have been running for 25 years, we see significant benefits to our customers such as reduction in operational costs and improved process efficiency resulting in financial benefits. An Insta-Pro technician will visit periodically to ensure your operators are maintaining best-in-class practices by helping retrain or refresh staff, getting parts costs down and optimizing your machinery to produce a more consistent, high-quality end product.
During this visit, an Insta-Pro technician will cover with your operators what to look for with worn parts and when to replace or rotate the parts to maximize parts wear. They will revisit proper operating procedures, correct operating temperatures and how to setup the internal barrel parts for different moisture levels in raw soybeans. The technician will also cover maintaining the shaft and bearing housing and motors to achieve the longest operating time possible. In between visits, the service tech assigned to your business will give you a call to discuss things and see how we can help.
I have seen a variety of issues and complications that could have been avoided with proper maintenance and continued training on operating procedures. This is how the Service Plus Program helps. There are different programs available, designed to fit your needs and budget. To learn more about this program, call 1-800-798-0951 or email Customer Service.