What is Automation and Why Should You Use It?
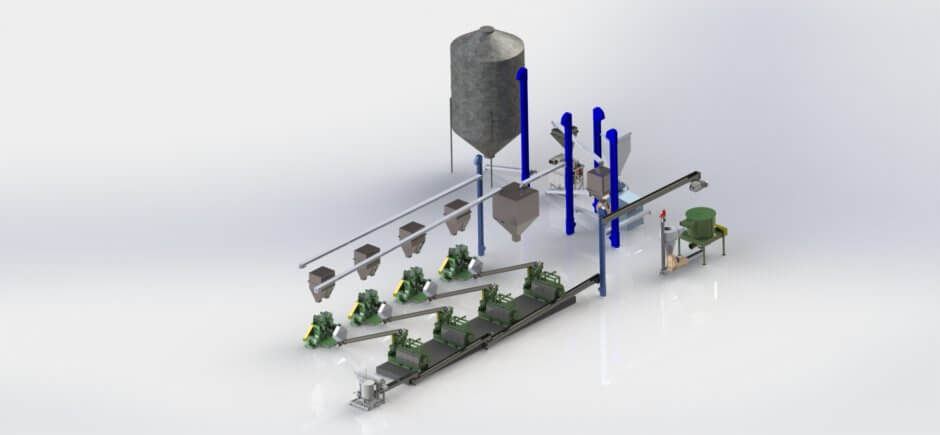
We hear more and more every day about automation. Making our lives easier, simplifying tasks, and increasing efficiency are the end goals, but what exactly is automation? What are some advantages of it and why should you choose to use it in your operation?
First, let’s define automation. This is a fairly new term used to describe performing a task automatically. In our industry, it’s mostly used to define how a plant operates and the logic used to do so. A common example is how most feed mills are controlled by a single point of operation which is used to turn the plant on and off. Automation allows equipment to be controlled in sequence and even remotely if needed.
Why should we consider automating a processing plant? The big advantage is that automation reduces the “human” influence of operation, making the process more consistent and less prone to errors. Try as we might, humans are inconsistent and forgetful. Using automation, a set of operating parameters can be defined, limiting the scope of what the equipment can do. Additionally, increasing safety is a major benefit, as a person could remotely operate equipment and reduce the chances of injury. Equipment malfunctions can be detected and mitigated right away, further reducing the need for human interaction.
Automation also helps reduce the staff required to perform tasks. Imagine a large plant consisting of several pieces of equipment spread amongst several floors. In order to manually turn on each piece of equipment, operators would have to go to several control panels, turning on individual motors to each piece of equipment or conveyor. Not only does this take a long time but should something go wrong or be out of sequence, the reaction time to fix the problem is greatly delayed. Automation can reduce this by defining the startup sequence and motor operating conditions, automatically adjusting should something happen. This can be done with less operators, reducing operational costs.
Obviously, an investment is required to do this. Smaller plants typically cannot justify the costs to do this, but different levels of automation do exist. Partially automating the plant can still yield big operational improvements and savings without the need to fully automate the entire plant. The most important aspect of automation is that it does need to be programmed by someone. For this reason, it is important to work with someone that has extensive knowledge of your operation. This becomes even more important with extrusion due to the increased number of variables involved. The goal here would be to automate the extrusion process. This is an exciting development for the future and one that Insta-Pro is actively pursuing. For now, working with a trusted partner who has extrusion experience is the key to success.