Calculating Drying Costs and Heat Needs
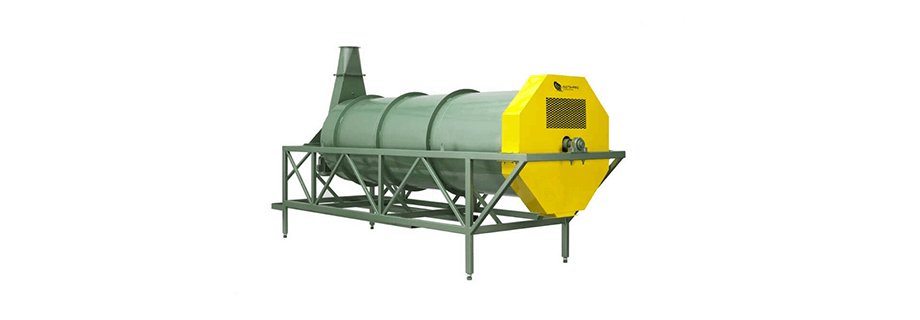
Plant investments can vary from initial capital investments to ongoing costs. This is why our sales team devotes time to conduct a feasibility analysis with you. We are then able to recommend a system that will allow you and your business to be successful.
For example, in fish and pet food production, a dryer/cooler is a must have. The moisture percentage of the product coming out of the extruder is higher than a typical safe level for storage, so drying/cooling equipment becomes a necessity. The question then becomes “How much energy do you need to do this? Below is a formulation that will assist in predicting the ongoing costs.
Incoming Water Amount
Let’s assume we have a product that leaves the extruder at 20% moisture at a rate of 2200 pounds/hr (1 metric ton/hr). We want to dry this down to 10% moisture coming out of the dryer/cooler so that it is safe for bagging and storage. It’s important to note the dry matter weight of the product as this will stay constant since we are only trying to remove moisture.
Solving for dry matter weight gives:
0.8 x 2200 lbs = 1760 lbs (dry matter)
This means we have 440 lbs of water in the product (2200-1760 or 20%)
Final Water Amount
In order to determine energy consumption of drying, we will need to determine how much water will be evaporated during the drying process. Since we know the dry matter weight (1760 lbs) and the final moisture percentage (10%), we can calculate the amount of water leftover in the final dried product.
We know that at 10% moisture, 90% of the final product is dry matter. We simply divide our dry matter weight by 90%:
1760 lbs / 0.9 = 1956 lbs
This is the final weight of the product coming out of the dryer at 10% moisture. We now know starting and ending weights of the product, so subtracting these will show how much water is evaporated during this process:
2200 lbs – 1956 lbs = 244 lbs (water/hr removed)
Note: we can verify this by subtracting this from our initial water weight (440 lbs) and dividing by ending weight (1956 lbs): (440 – 244) / 1956 = 10%
BTUs
As a rule of thumb, it takes about 1500-1800 BTU to vaporize one pound of water. Let’s assume it takes 1800 BTUs for a conservative calculation. We need to remove 244 lbs of water per hour, so the amount of BTUs required is:
1800 BTU/lb x 244 lbs/hr = 439,200 BTU/hr
You can use this in cost estimations for utilities and equipment sizing (dryer/coolers, boilers, etc). Initial capital investments are important considerations, but ongoing costs such as this must be taken into account as well. This is a perfect opportunity for a feasibility analysis!